OPRACOWANIE KOMPLEKSOWEJ TECHNOLOGII AKTYWNEGO I PASYWNEGO ZABEZPIECZENIA ANTYKOROZYJNEGO INSTALACJI WZBOGACANIA RUD METALI NIEŻELAZNYCH
Projekt nr: CuBR/III/1/NCBR/2017
Akronim: CUBR III
Projekt dotyczy opracowania kompleksowej technologii aktywnego i pasywnego zabezpieczenia antykorozyjnego instalacji wzbogacania rud metali nieżelaznych znajdujących się w O/ZWR KGHM Polska Miedź SA. Zagadnienie ma obejmować selekcję materiałów, ochronę elektrochemiczną i dostosowaną do niej pasywną ochronę powłokową. Końcowym efektem ma być wdrożony w skali przemysłowej system ochrony wybranych instalacji wzbogacania rud. Rezultatem będzie zwiększenie efektywności procesu wzbogacania poprzez wydłużenie okresu eksploatacji instalacji wzbogacania rud dzięki wdrożeniu opracowanych rozwiązań antykorozyjnych.
Oddział Zakłady Wzbogacania Rud (w skrócie O/ZWR) stanowi jeden z kluczowych elementów w technologii produkcji miedzi. Sprawne zarządzanie O/ZWR wiąże się z ciągłą poprawą efektywności produkcji poprzez rozwój procesu technologicznego, szybkość reakcji na nowe możliwości oraz zaistniałe problemy, generowanie i wprowadzanie innowacji. Jako poprawę efektywności procesu produkcji, poza wprowadzaniem nowych, nowoczesnych urządzeń, rozumie się również optymalizację pracy urządzeń już istniejących, jak również wydłużanie okresu ich eksploatacji. Procesy degradacyjne występujące w instalacjach O/ZWR powodują wymierne koszty związane zarówno z pracami remontowo – naprawczymi jak i te, które wynikają z przerw w produkcji.
Dla oceny procesów degradacyjnych instalacji wzbogacania surowców mineralnych ZWR niezbędne jest stworzenie szczegółowego opisu i charakterystyki wszystkich elementów ciągu technologicznego wraz z określeniem wpływu ich niezawodności na ciągłość prowadzenia procesu wzbogacania (zadanie 1). W ramach tego zagadnienia zostaną wytypowane najsłabsze elementy urządzeń do wzbogacania, dla których koniecznym jest dostosowanie ochrony powłokowej lub prawidłowo dobranych materiałów. W tym zadaniu opracowane zostaną główne metody badań, kryteria oceny oraz szczegółowe oznaczenie korozyjności atmosfery w zależności od lokalizacji danego fragmentu instalacji i zadań procesowych prowadzonych na danym obszarze. Przegląd aktualnego typu zabezpieczenia antykorozyjnego i materiału konstrukcyjnego uzupełniony wynikami wymienionych badań umożliwią profesjonalne wytypowanie szeregu alternatywnych materiałów i technologii powłokowych, które zostaną zbadane i zweryfikowane nie tylko od strony technicznej, ale również ekonomicznej w dalszych zadaniach projektu. Uzyskane z analiz i badań dane stanowią wytyczne do selekcji nowych systemów powłokowych.
Celem badań materiałowych (zadanie 2), będzie określenie odporności na korozję oraz zużycie ścierne różnych rodzajów powłok ochronnych pokrywających elementy przepływowe instalacji wzbogacania rud metali nieżelaznych. Na przykładzie maszyn flotacyjnych mogą to być łopatki uspokajacza zespołu aeracyjnego flotownika, dla których określona zostanie przydatność tworzyw w budowie podzespołów maszyn flotacyjnych. W kolejnych etapach pracy te same właściwości zostaną przebadane dla powłok metalowych nanoszonych za pomocą nowoczesnych metod natryskiwania cieplnego i napawania laserowego. Opcjonalnie uwzględniony będzie system metalowo – malarski. Oddzielnym zagadnieniem będzie rozważenie wymiany niektórych elementów instalacji z materiałów metalowych na tworzywa sztuczne. Ten trend jest już w KGHM uwzględniony dla większości rurociągów.
Drugim obiektem do zaproponowania wymiany dotychczas stosowanych powłok jest ta część infrastruktury ZWR, która dotyczy elementów konstrukcyjnych, na których umieszczone są urządzenia produkcyjne, konstrukcji wsporczych, belek wspierających podesty i innych podobnych elementów instalacji. W tym przypadku selekcja systemów powłokowych będzie wynikać z oznaczeń korozyjności atmosfery na różnych poziomach ciągów technologicznych. Z porównania wyników badań laboratoryjnych właściwości ochronnych potencjalnych powłok i systemów powłokowych, w tym powłok metalizacyjno – malarskich oraz wcześniej badanych powłok metalowych i cermetalowych, wybrane zostaną te warianty, dla których w następnym zadaniu badawczym opracowana zostanie technologia demonstracyjna na wybranych urządzeniach lub/i elementach konstrukcji ZWR. W tym zadaniu wszystkie próbki zostaną zbadane w laboratoriach członków Konsorcjum. Dokonany wcześniej wybór potencjalnych powłokowych systemów ochronnych zweryfikowany w badaniach laboratoryjnych w zadaniu 2, wymaga opracowania szczegółowej technologii ich nanoszenia/wytwarzania na konkretnych elementach instalacji i w danej lokalizacji. Działania te będą zrealizowane w zadaniu 3. W niniejszym wniosku proponowane są technologie natrysku cieplnego (łukowe, naddźwiękowe, plazmowe), technologie deponowania laserowego oraz technologie nanoszenia powłok organicznych metodami zależnymi od rodzaju materiału malarskiego oraz we wszystkich wymienionych przypadkach – w zależności od rodzaju konstrukcji. Wszystkie wymienione technologie wymagają odpowiedniego przygotowania powierzchni, którym w większości będzie obróbka strumieniowo-ścierna, ale w zależności od szczegółów wykonania dobierane będą zarówno rodzaje ścierniw, jak i parametry technologiczne. W przypadkach specjalnych takich jak miejsca trudnodostępne dla strumienia ścierniwa, przewiduje się chemiczne przygotowanie powierzchni. Do potencjalnych elementów konstrukcji przeznaczonych do zabezpieczania za pomocą systemów powłok organicznych zarówno wersji samodzielnej, jak i z powłoką metalową (metalizacyjną) należą części konstrukcji wsporczych urządzeń, zewnętrznych powierzchni maszyn flotacyjnych, hydrocyklonów oraz wybranych elementów infrastruktury ZWR. Potencjalnymi elementami konstrukcji do zastosowań metalizacji natryskowej oraz deponowania laserowego w ZWR są sita, przesiewacze, wlewy młynów, przesypy, elementy hydrocyklonów, wirniki łopatek wentylatorów, elementy transportu urobków (rudy, skały itp.) wykładziny podawcze szuflad, czerpaki nadawy, zawory odcinające, elementy młynów do mielenia.
W zadaniu 4 realizowane będą prace związane z technologią ochrony aktywnej, czyli ochrony elektrochemicznej. Potencjalne obiekty objęte ochroną elektrochemiczną wraz z dostosowanym zabezpieczeniem powłokowym to wewnętrzne powierzchnie hydrocyklonów, maszyn flotacyjnych, części klasyfikatora spiralnego, jak również zbrojenia konstrukcji żelbetowych ze szczególnym uwzględnieniem zespołu osadników Dorra oraz ścian rząpi. Jednakże konkretny wybór obiektu do zabudowy instalacji ochrony katodowej nastąpi w wyniku szczegółowej analizy warunkówużytkowania tego obiektu. W pracach weźmie udział wyłoniona w drodze przetargu firma. Zadanie 4 finalizuje również projekt od strony technologicznej tzn. wykonania dokumentacji materiałowej i technologicznej wybranych wersji zabezpieczeń przeciwkorozyjnych oraz uzupełnia merytorycznie wyniki całego projektu w zagadnieniu związanym z interpretacją mechanizmu degradacji materiałów stosowanych w ZWR.
Projekt realizowany przez konsorcjum w składzie:
- Instytut Mechaniki Precyzyjnej – Lider
Konsorcjanci:
- Instytut Metali Nieżelaznych
- Plasma System S.A.
- Akademia Górniczo-Hutnicza, Wydział Metali Nieżelaznych
Kierownik projektu: dr Lech Kwiatkowski
Kierownik projektu ze strony IMN: dr inż. Bożena Skorupska
Termin realizacji projektu: 2017.05.01 – 2020.04.30
Całkowity koszt realizacji projektu : 5 057 187 zł
w tym wysokość dofinansowania: 2 397 343,50 zł
Projekt współfinansowany przez Narodowe Centrum Badań i Rozwoju i KGHM Polska Miedź SA
w ramach Wspólnego Przedsięwzięcia CuBR – wsparcie badań naukowych oraz prac rozwojowych dla przemysłu metali nieżelaznych.
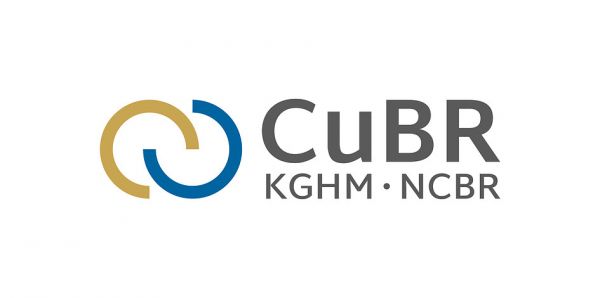
