Centre of Metallurgy
About
Centre of Metallurgy
Our activity
The Metallurgy Center deals with extractive metallurgy of non-ferrous metals. We develop, among others, technologies for pyrometallurgical processes for the production of metals from
- ores
- concentrates
- scrap and waste
- fire refining of metals
Research offer in the field of extractive metallurgy
- methods of preparing the charge for metallurgical processes through, among others, briquetting, granulation, sintering and roasting
- development of methods for briquetting and granulating various materials together with the selection of the optimal type of binder
- process designs and technical and technological analyses of existing and new processes together with design assumptions
- development of technologies for the recovery of non-ferrous metals from concentrates and all types of secondary raw materials (technology concepts, selection of devices and parameters, design assumptions)
- methods for refining non-ferrous metals from impurities
- methods for obtaining chemical compounds and useful alloys from semi-finished products and waste containing non-ferrous metals
- mathematical modelling and development of algorithms for controlling metallurgical processes and decision support systems
R&D
Research Groups
Zinc and Lead Metallurgy Research Group
Contact
Head: Ryszard Prajsnar, PhD
tel. +48 32 2380 466
Metallurgical Process and Energetics Modelling Research Group
Contact
Head: Katarzyna Klejnowska, PhD
tel. +48 32 2380 666
R&D
Laboratories
Laboratory of Metallurgical Processes Fundamentals
The Laboratory of Metallurgical Processes Fundamentals analyzes issues related to the theory of metallurgical processes, such as the study of phase systems
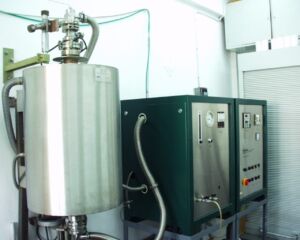
Laboratory of Metallurgical Processes
The main idea of the laboratory is to carry out work related to high-temperature processing of primary and secondary materials containing non-ferrous metals using pilot metallurgical units
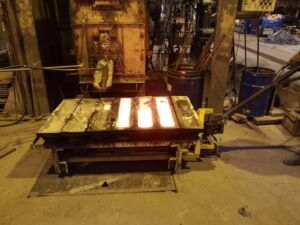
Implemented projects
Cooperation with the industry
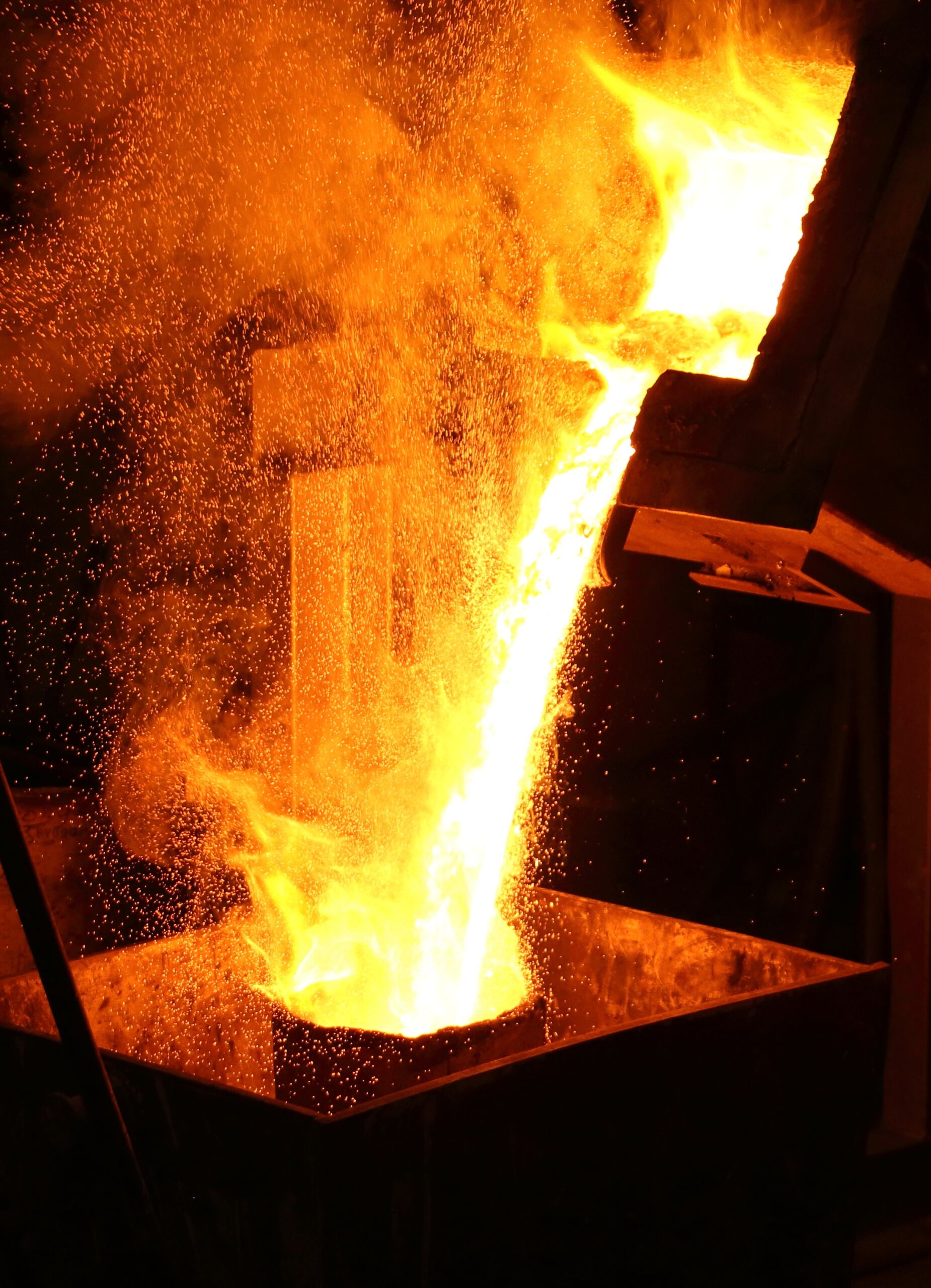
Pyrometallurgy, metallurgy
In cooperation with industry, we have implemented projects whose results have a real impact on the business results of our partners.
Some of them are:
- development of technology for decopperizing slag from a flash furnace in an electric furnace
- development of a new technology for converting CuPbFe alloys
- modernization of the cooling and dust removal system for technological gases from an electric furnace
- development of a new method for economic firing of rotary furnaces for copper fire refining
- development of a new technology for processing converter slag from CuPbFe alloy refining in order to recover lead from it
- development of technology for roasting part of copper concentrates in a rotary furnace in order to remove organic carbon from them
- development and implementation of a comprehensive technology for the recovery of valuable metals from semi-finished products of raw lead refining
- development and application of technology for selective smelting of lead-bearing fractions from battery scrap processing
- development and implementation of technology for the production of zinc white from charges with the participation of secondary zinc
- development of technology and launch of production of new lead alloys for batteries and coatings cables
- development on an industrial scale of a new method of utilizing lead-zinc dust from copper smelting by processing it using the pyrometallurgical method, with recovery of Zn, Pb and Cu
- development of a technology for processing lead slag into an ecologically safe silicate slag with low heavy metal contents, potentially suitable for economic use
- development of a technology for pyrometallurgical utilization of ecologically hazardous waste slag from tin production in the TSL process
- development of a technology for reductive roasting of a granulated mixture of waste dust and sludge from iron smelting in a rotary kiln
- development of an energy-saving technology for producing qualified zinc white from primary, secondary and zinc waste
Recycling
- cooperation with companies involved in waste processing and recycling
implementation of technology and construction of an experimental installation for processing waste lithium-ion batteries - implementation of technology for obtaining pure metallic zinc and brass granulates obtained during mechanical processing of zinc-carbon and alkaline batteries and construction of a purification and separation line
- development and implementation of technology for briquetting waste from mineral wool production
- development of an analytical method for determining the content of metals in polymetallic granulates of electronic and electrical scrap
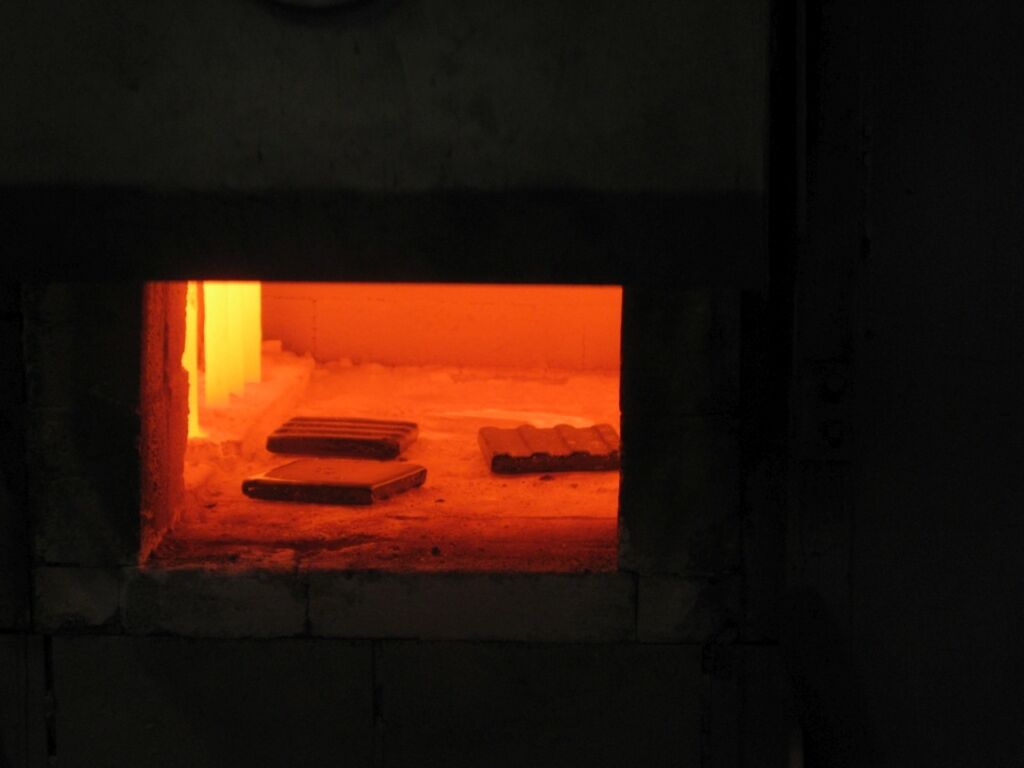
Infrastructure
Equipment
The Center is equipped with research, control and measurement equipment, as well as experimental devices and installations.
The most important equipment includes:
- Thermobalance TA1 by Metller with a vacuum system
- Testing machine EDZ – 40
- Furnace for testing the softening and melting temperatures of oxide materials using the Bunte-Baum-Reerink method
- Viscometer LVDV-II+ DIGITAL by Brookfield Engineering Laboratories, INC. combined with a chamber furnace F 46 120 CM
- High-temperature viscometer Rheotronic II by Theta with a measuring head by Brookfield DV III LV
- Electric tube furnace type PPR–140/1300
- Chamber furnace type F 46120 CM by Thermolyne
- Tubular furnace FRV – 70 – /400/1700 with an added system of vacuum-tight closures allowing for operation in a vacuum version, as well as in a strictly controlled gas atmosphere in cooperation with a partial pressure regulator,
- Two rotary furnaces: laboratory electric and experimental heated with natural gas
- Rotary-shuttle furnace for processing lead- and zinc-bearing waste
- Arc-resistance furnaces designed for melting materials based on Cu, Zn, Pb with a capacity of 30, 50 and 120 kg of slag and a power of 80 and 100 kVA
- Melting and refining furnace designed for melting and refining low-melting materials
- A shaft furnace with a vertical oil-air lance for conducting metallurgical processes with a capacity of approx. 200 kg of slag together with a process gas dedusting system
- A process gas analyzer
- Oxygen installation
Waste recycling:
- Sturtevant disc crusher
- High-speed beater crusher
- Wichary AZ 05F knife crusher
- Retsch SM300 crusher
- Fritsch knife crusher
- Two-roll crusher
- Hammer crusher
- LMN knife mill for polymeric materials
- Laboratory ball mill
- Innovox portable XRF analyzer
- Cogelme electrodynamic separator
- Dostmann P 755-log process parameter meter (e.g. temperature)
- Metronic IP-30 process parameter meter (18 measurement points)
- Universal furnaces SNOL 1150oC
- Laboratory winding separator
- Laboratory multi-deck separator
- Laboratory drum separator
- Laboratory shaker-air separator
- 2 Low-temperature pyrolysis furnaces with exhaust gas afterburning system – laboratory
- Opta-Tech microscope max. surface 45x
- Liquid nitrogen device
- FRITSCH PULVERISETTE 19 universal cutting mill
- FRITSCH LABORETTE 27 rotary sample divider
- FRITSCH LABORETTE 24 vibrating trough feeder
- FRITSCH PULVERISETTE 9 vibrating disc mill
- PULVERISETTE 0 vibrating micro mill
- Calorimeter
Contact us